Production Process
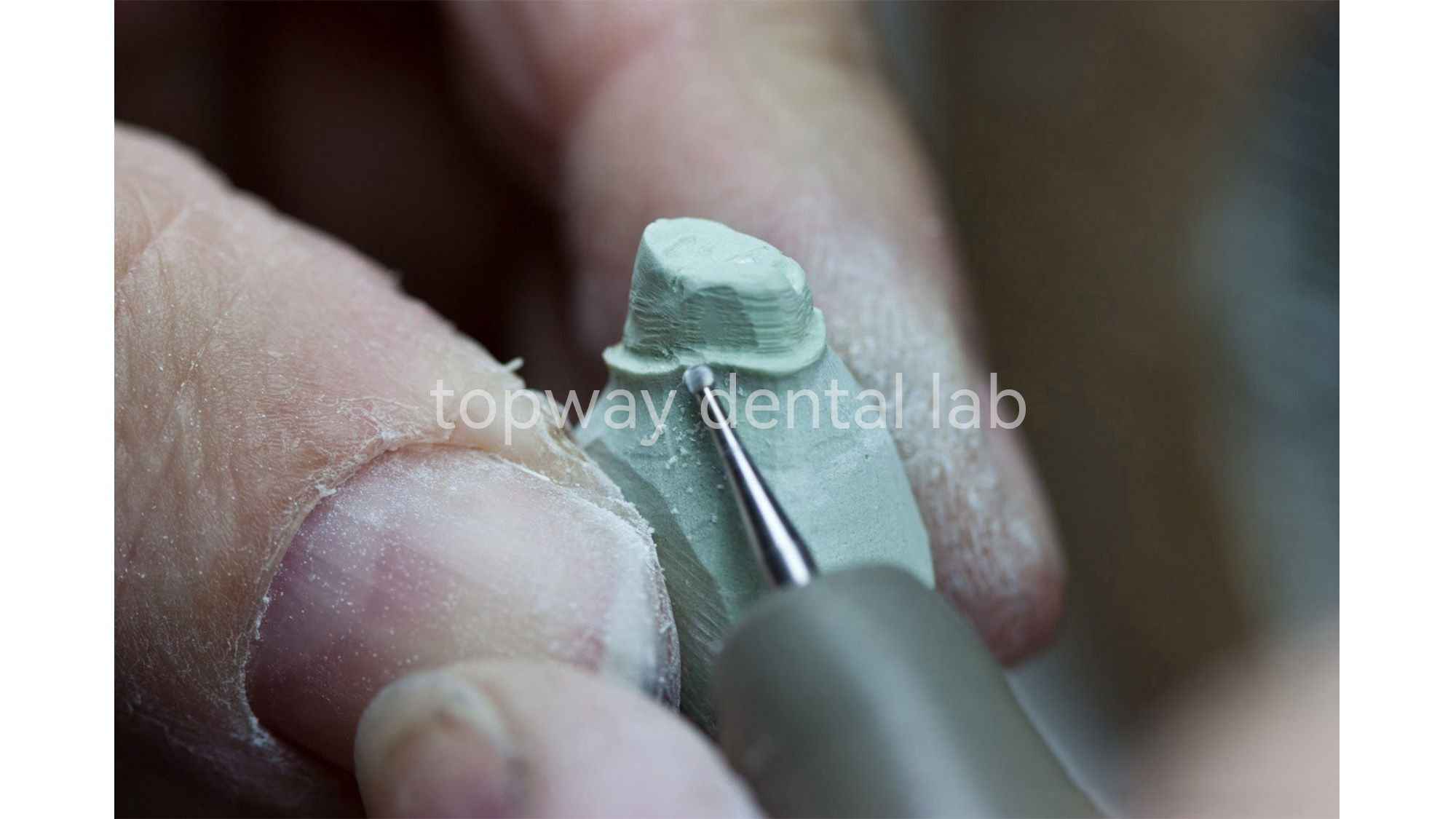
Pour model,trim margin,articulate occlusion
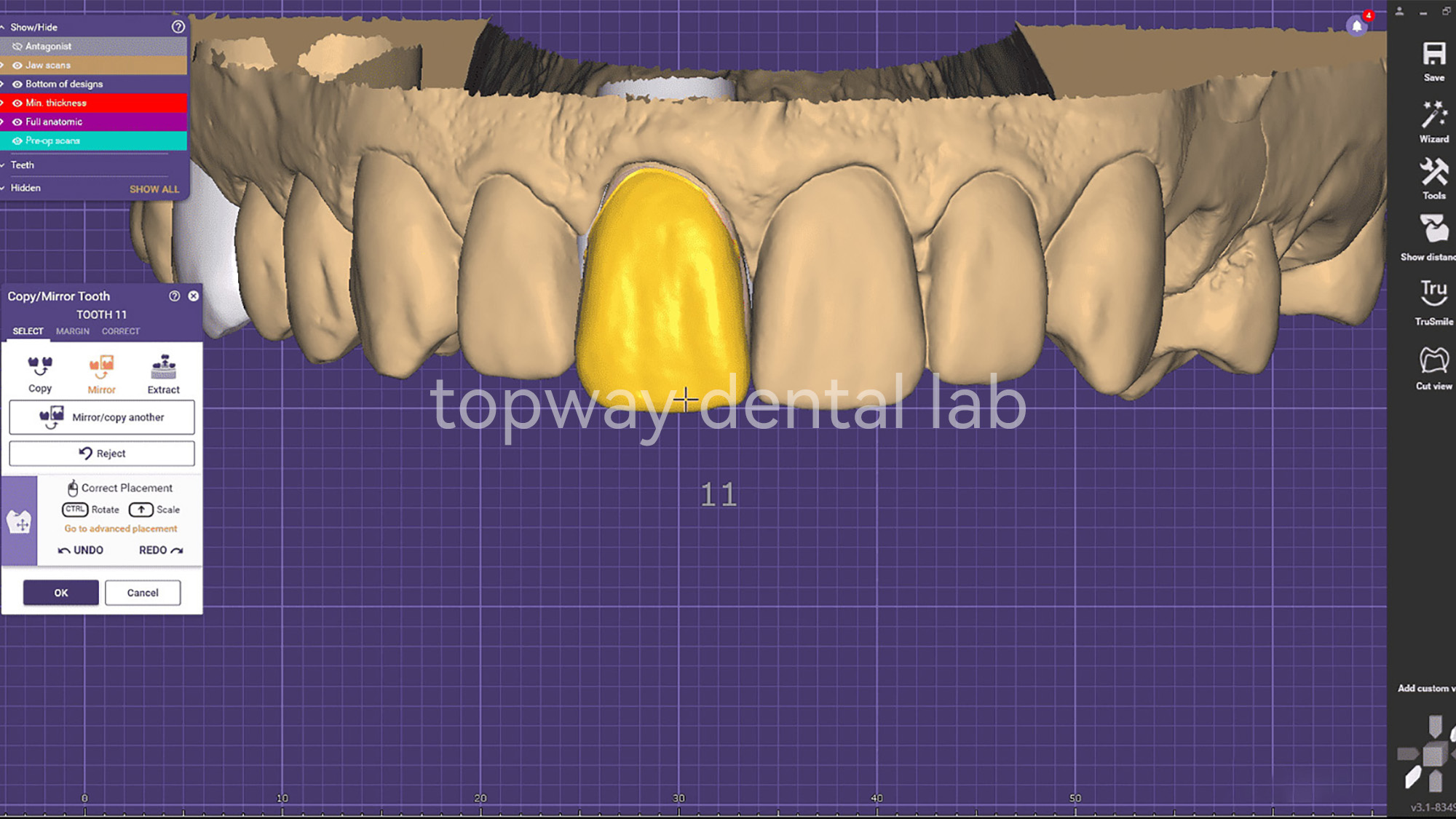
Model scan and design
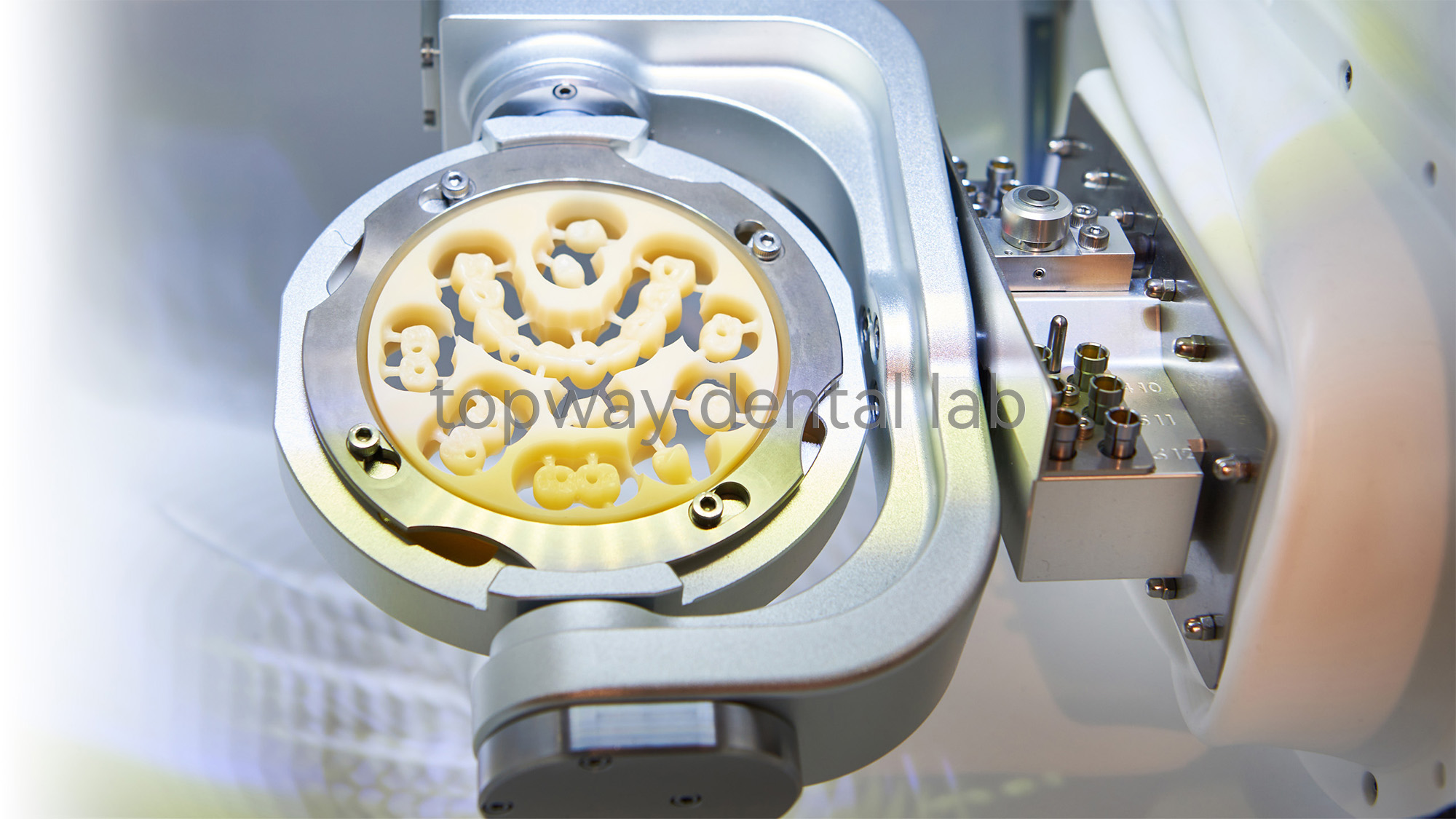
Milling
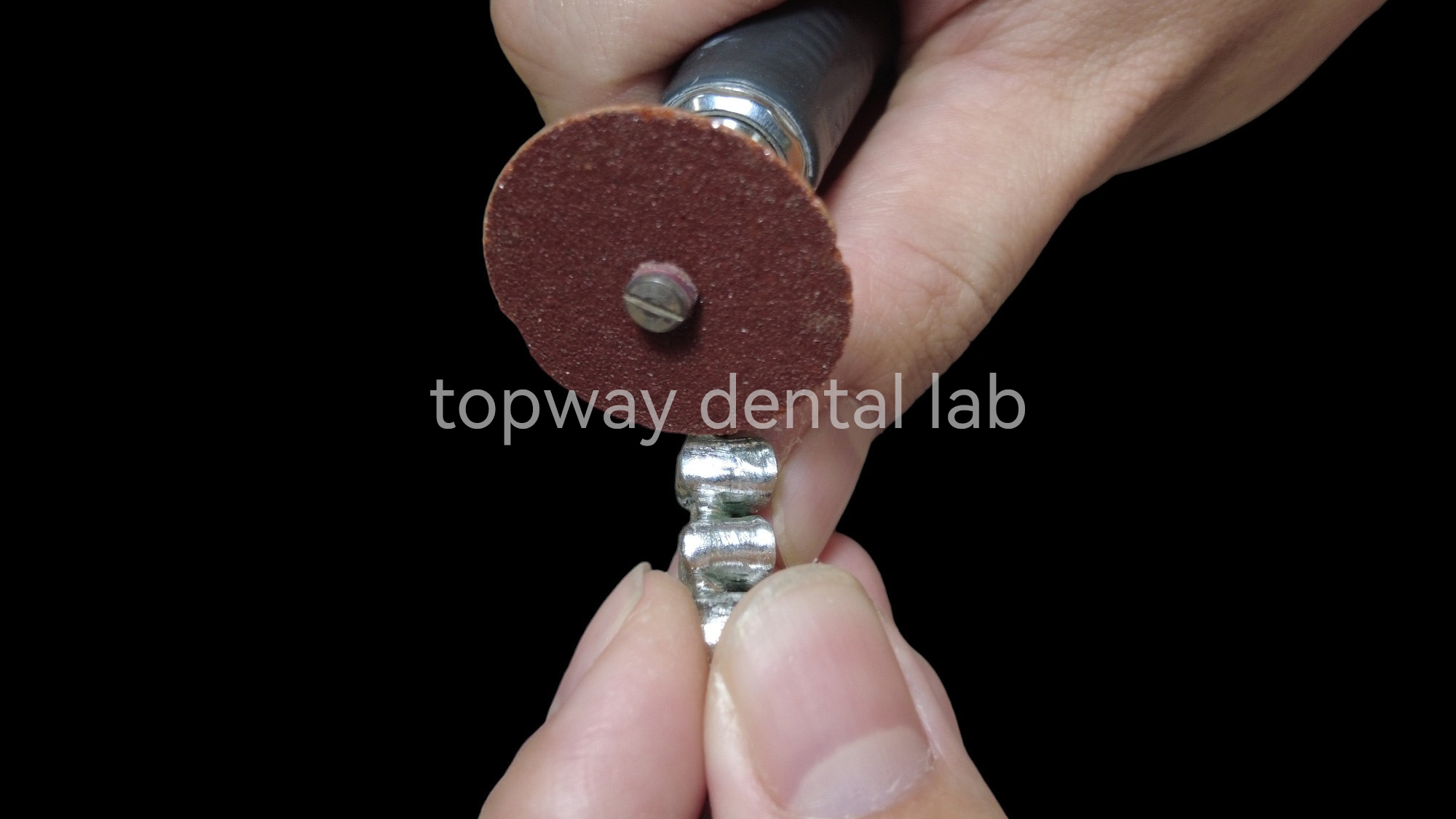
Coping milling
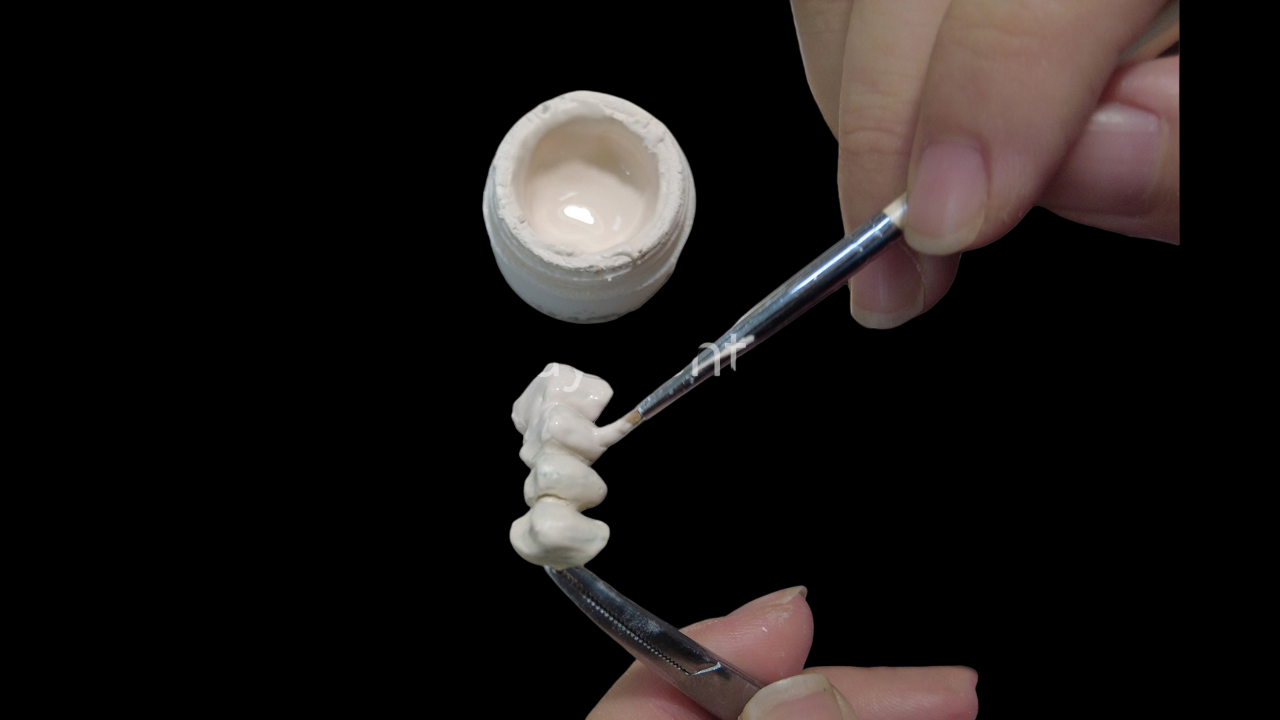
OP
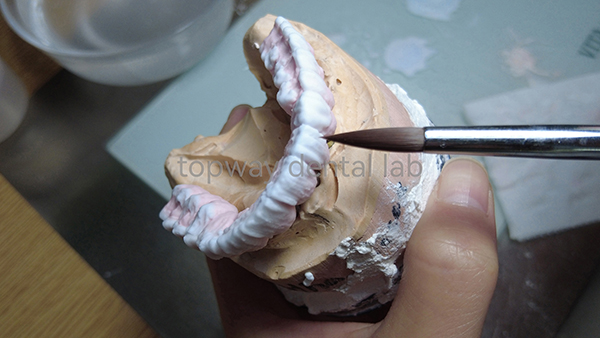
Stack the tooth shape with porcelain powder,then Sintered
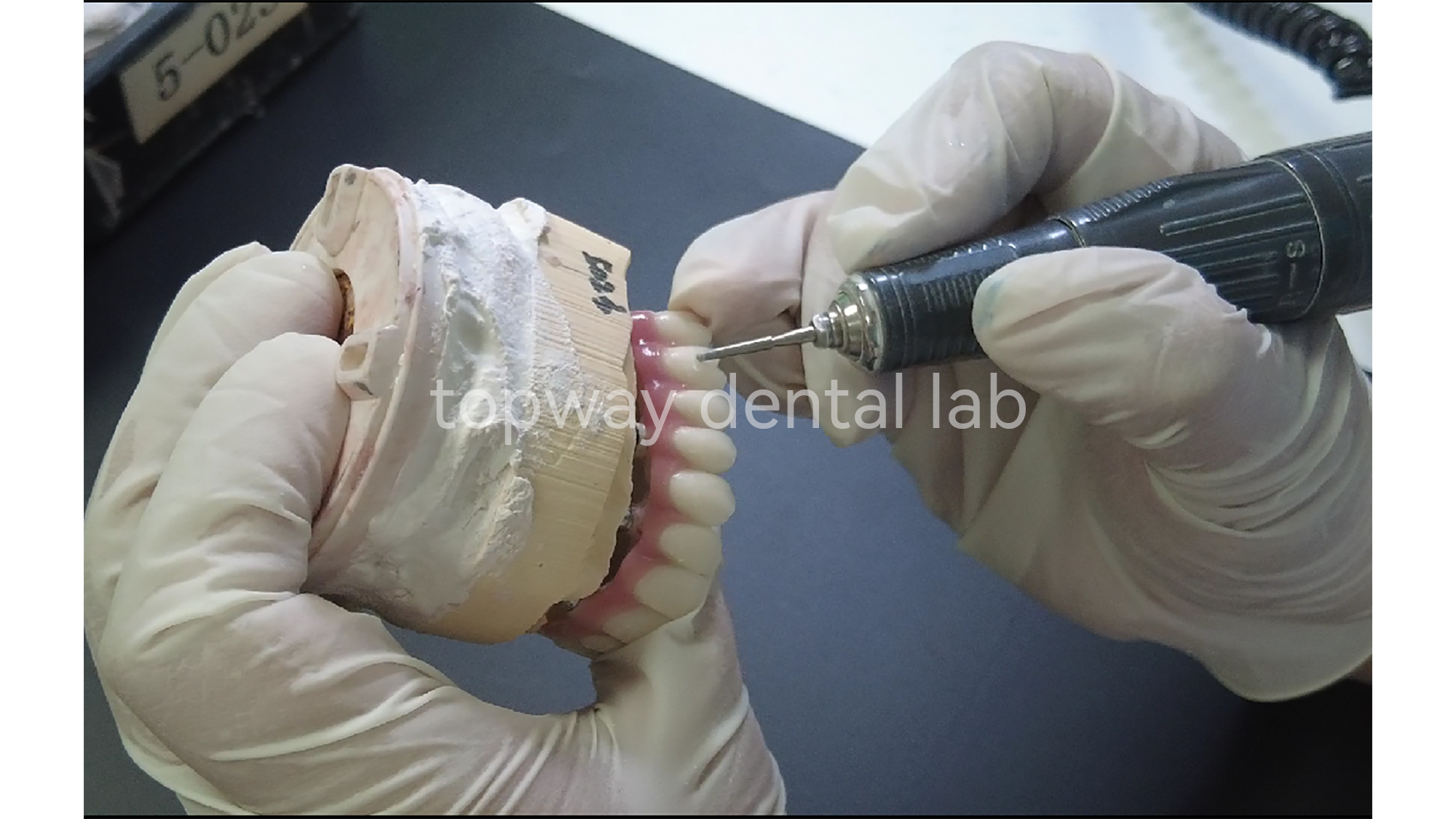
Mill final countor,contact,occlusion
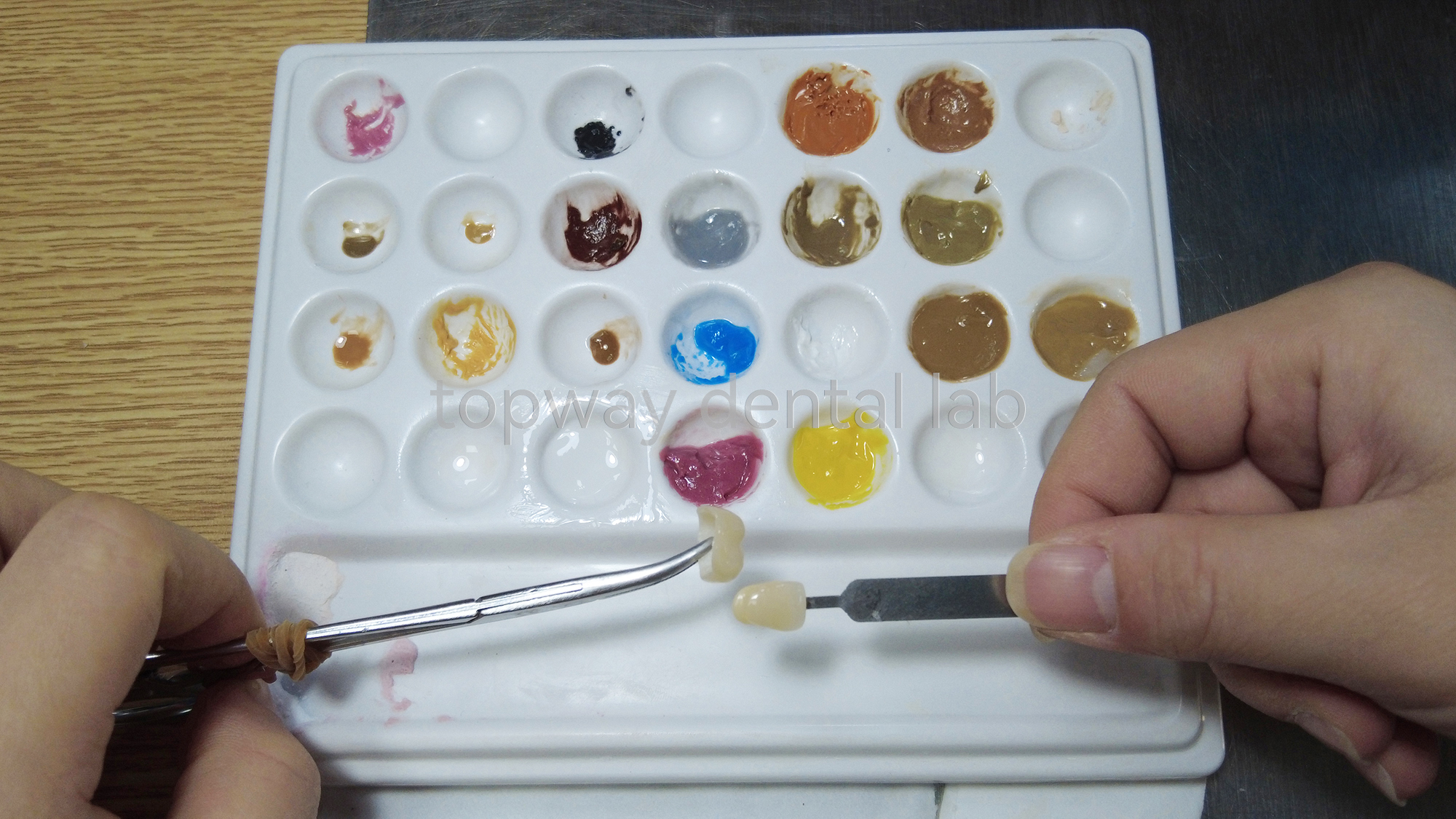
Coping milling
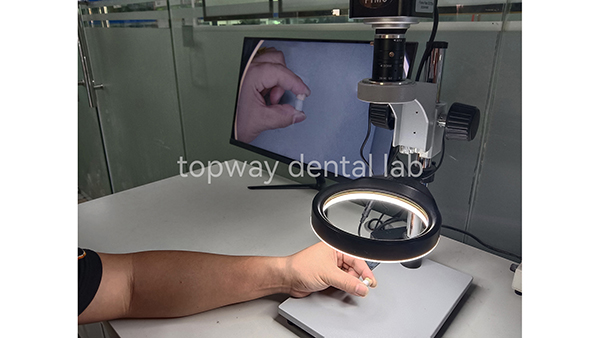
Final Examining
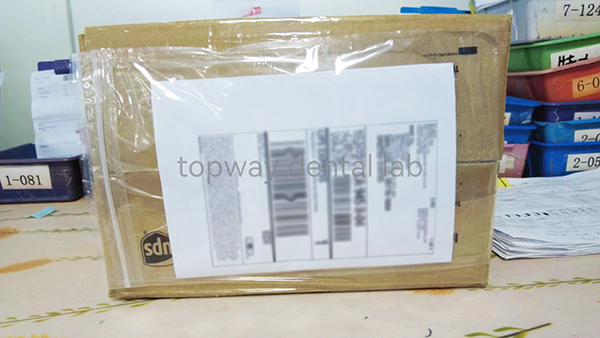
Pack Up Then Return
Turnaround Time
Fixed Crown & Bridges | In Lab Days |
PFM Crown & Bridge <4 units | 3-4 days |
PFM Crown & Bridge >4 units | 4-5 days |
Metal Try-in / Full Cast Crown | 2 days |
Porcelain Finish | 2-3 days |
Post & Core+PFM | 3-4 days |
Temporary Crown & Bridge | 2 days |
E-max Crown & Veneer | 3 days |
Zirconia Crown & bridge <4 units | 3-4 days |
Zirconia Crown & Bridge >4 units | 4-5 days |
Full Contour Zirconia Crown & Bridge<5 units | 2-3 days |
Full Contour Zirconia Crown & Bridge>5 units | 3-4 days |
Implant Crown & Bridge<4 units | 4 days |
Implant Crown & Bridge>3-6 units | 4-5 days |
Implant Crown & Bridge>6 units | 5-6 days |
Removables | In Lab Days |
Cast framework | 2-3 days |
Cast framework with Wax Rim | 2-3 days |
Cast framework with set up | 3-4 days |
Cast framework with denture finish | 4-5 days |
Set up only | 2-3 days |
Finish denture | 2-3 days |
Set up and finish | 3 days |
Fixed Combo with Removable | In Lab Days |
Fixed & Cast only | 2-3 days |
Fixed & Cast and denture | 3-4 days |
Tooth Box Classification
The order tracking group places the dental lab cases in the corresponding boxes according to the shipping time.
Production is carried out in sequence according to the color of the boxes.
Shipping Management
Group will write the customers and their corresponding delivery times for the following day on the shipping whiteboard
Production should make personnel and time arrangements in advance according to the shipping schedule for the following day
The production department arranges the production sequence for each customer based on the shipping time
Shelf Management
3 types of cases (trouble cases, rework cases and urgent cases) are placed on the top shelf for technicians to allocate and produce them as quickly as possible.
Unfinished dental cases are placed on the shelf in order of their shipping dates, from top to bottom. The team leader starts allocating denytal cases from the topmost layer.
Order Tracking – System Management
1.The corresponding process in which it is located.
2.Corresponding production order number
Each item can be traced to its corresponding production process, producer, and completion time.
The tracking clerk will monitor the progress of each item in the customer’s package.
Order Tracking – Form Management
The customer provides an urgent list, and the document clerk tracks the progress of urgent dental cases until they are shipped on time.
Quality & Progress Assurance
1.The Tracking Department Issues Production Plan First, the tracking department divides the dental cases into corresponding shipping boxes based on customer shipping requirements, with different colors representing different shipping times.
2.Production are controllable and traceable Each team classifies the dental cases in order of shipping using the boxes and places them on their own shelves. Team members then produce the dental cases in the specified order. Team leaders are responsible for internal returns and urgent items, arranging for their immediate production, and following up until the dental cases are handed over to the next team, and then handing over to the next team leader.
The company also has video surveillance to ensure that the production process and behavior are controllable and traceable.
3.Shipping Rate Analysis Tracking clerks calculate the shipping rate and compile a list of delays based on the planned and actual shipping situation. Production assistants then investigate the reasons for delays based on the shipping rate and delay list, analyzing responsibility down to the team level.
4.Team Leader Assessment Production clerks summarize daily delays, track the progress of each team, and use this to assess the management work of team leaders, directly impacting performance.
Production Quality Management
Arrival Inspection
![]() |
![]() |
![]() |
![]() |
Inspection of implant components | Inspection of the Prep teeth and margin | Inspection of the model | Inspection of the wax bite |
Process Inspection
![]() |
![]() |
![]() |
![]() |
Pre-design bite check | Check the fit | Check the margin | Bite check when mill porcelain |
Final Quality Inspection
![]() |
![]() |
![]() |
![]() |
![]() |
Check fit | Check margin | Check the occlusion | Check contact | Check the shade |
Quality Inspection Standard Grades |
||
A | Perfect, direct shipment | |
(1) Perfect edge fit, no overhang, no underlying color (2) Perfect positioning (3) Vivid form (4) Good color layering (5) Surface without defects (6) Bite contact meets customer requirements (7) No functional defects, perfect arrangement |
||
B | Requires rework | |
(1) Rough (2) Bubbles, small holes, black spots (3) Slightly misaligned (4) Missing porcelain in long bridge tooth gaps, minor edge chipping |
||
C | Must be redone | |
(1) Not made according to design requirements (2) Unable to be positioned (3) Incorrect edges (4) Incorrect color (5) Deformed |