Topway dental lab located in Shenzhen,China. is the full service lab privately owned full dental restoration laboratory in the country. With more than 19 years in business, more than 100 capable technicians and over 3000 m2 of manufacturing space, we are able to serve a all world clientele of dental lab , clinic, dental studio ,dentists.
We work in tandem to make decisions that propel us into the future. Many of these decisions revolve around 3D workflows and process automation.
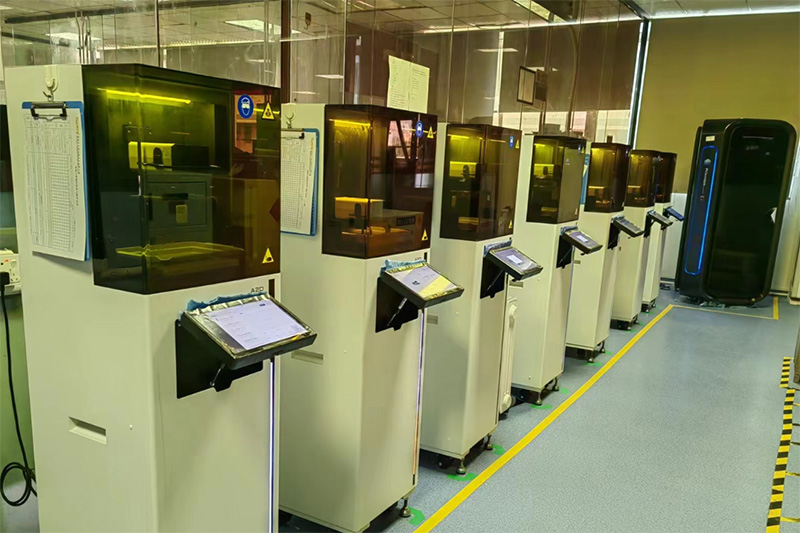
A large proportion of our printer fleet are HeyGears models. Where there is a range of machines available for printing, those providing added benefits quickly stand out from the pack. For Topway dental Lab, the most impactful factors of the HeyGears UltraCraft A3Ds are their capacity and their automation, both wrapped up neatly in a printer with a compact footprint.
To combat this drain on human and time resources, Topway dental lab employs the HeyGears workflow to introduce automation wherever possible. Using HeyGears Cloud, technicians are able to automatically generate print trays from uploaded STL files, drastically reducing the time required to organise files for efficient printing, and can quickly assign prepared print jobs to individual printers—from the same portal. Plus, several print jobs can be queued to run consecutively, optimising the technician time rather than having to restart the process at the end of each job. The next job in line will simply start when the job before it has finished (Fig. 3).
In the event that a higher priority file arrives, jobs can be easily rearranged with the rush order feature in the software, allowing the technician to reprioritise on the go. This automation ensures that time saved by technicians in preparing and delegating jobs ahead of time will never be lost when an inevitable rush order comes through the laboratory. This is an important point: automating 3D printing does not massively change your process; it simply streamlines it. Rush orders are an everyday occurrence in the laboratory, and this software automation allows us to work around them while still working more efficiently.
With HeyGears printers, an automatic arm attachment removes the plate, clears the models and resets the plate for the next job. Models are gathered in a collection bin that makes the post-processing of many jobs at once a simple task—especially when the models can be removed while the printer continues to run. As soon as the plate is back in place, the software begins the next job in the queue line, allowing printers to continuously run unattended, even in off-duty hours. As any laboratory owner knows, technician time is a limited resource, and the ability to run the same number of jobs we do during the day even when the doors are closed for the night has been a massive advantage to our print capacity.
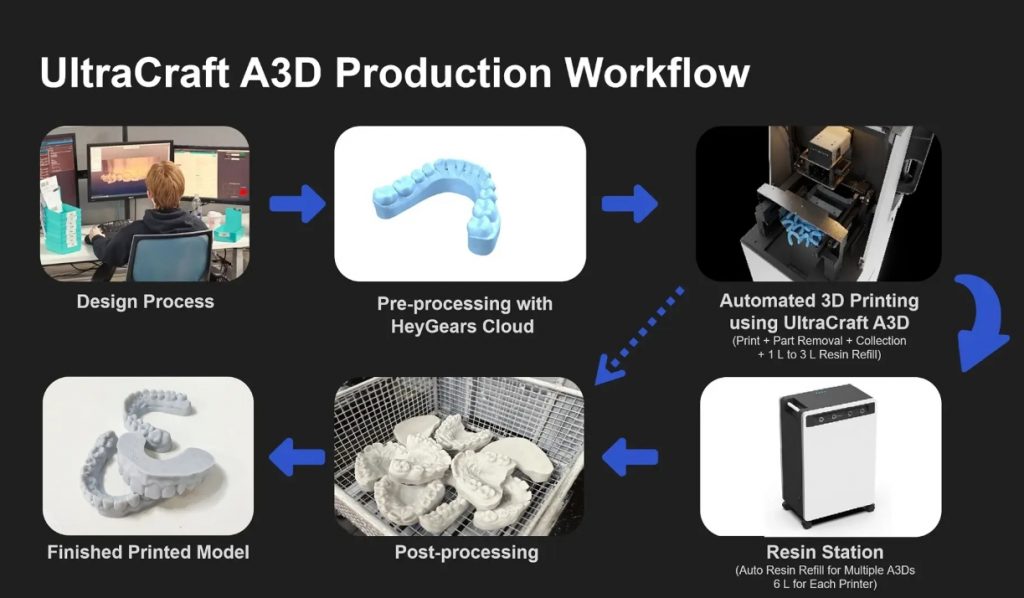
I believe that the world of 3D printing will continue to see more and more integrated automations. STL file receipt is being improved to remove manual inputs and improve quality, and digital design software is continually being reanalysed and infused with more artificial intelligence to speed up processes. Whereas HeyGears has already removed much of the manual labour of physical 3D printing, I think we will continue to see advancements—in software, when it comes to nesting and build platform design; in hardware, with technicians being able to step further back from actively monitoring machines; and in material resources, by being able to cut out fabrication entirely with direct printing. Within a decade, we may not even recognise what used to be basic, everyday processes because they have been so removed from workflows by automations.
In the China Dental laboratory: Automation rules the future of 3D printing.